Plastic extrusion for detailed profiles and custom designs
Plastic extrusion for detailed profiles and custom designs
Blog Article
A Comprehensive Guide to the Refine and Benefits of Plastic Extrusion
In the vast world of production, plastic extrusion becomes a important and extremely effective process. Altering raw plastic right into constant profiles, it deals with a huge selection of industries with its remarkable adaptability. This guide aims to illuminate the elaborate actions associated with this approach, the sorts of plastic suitable for extrusion, and the game-changing benefits it gives the sector. The occurring conversation guarantees to unravel the real-world impacts of this transformative procedure.
Recognizing the Fundamentals of Plastic Extrusion
While it might show up complex initially glance, the procedure of plastic extrusion is basically straightforward - plastic extrusion. It is a high-volume production strategy in which raw plastic is melted and shaped right into a constant profile. The process begins with the feeding of plastic product, in the form of granules, powders, or pellets, into a heated barrel. The plastic is then melted making use of a mix of warm and shear, applied by a rotating screw. When the molten plastic gets to the end of the barrel, it is forced via a little opening called a die, forming it into a wanted form. The designed plastic is then cooled down, solidified, and cut right into wanted sizes, completing the procedure.
The Technical Refine of Plastic Extrusion Explained
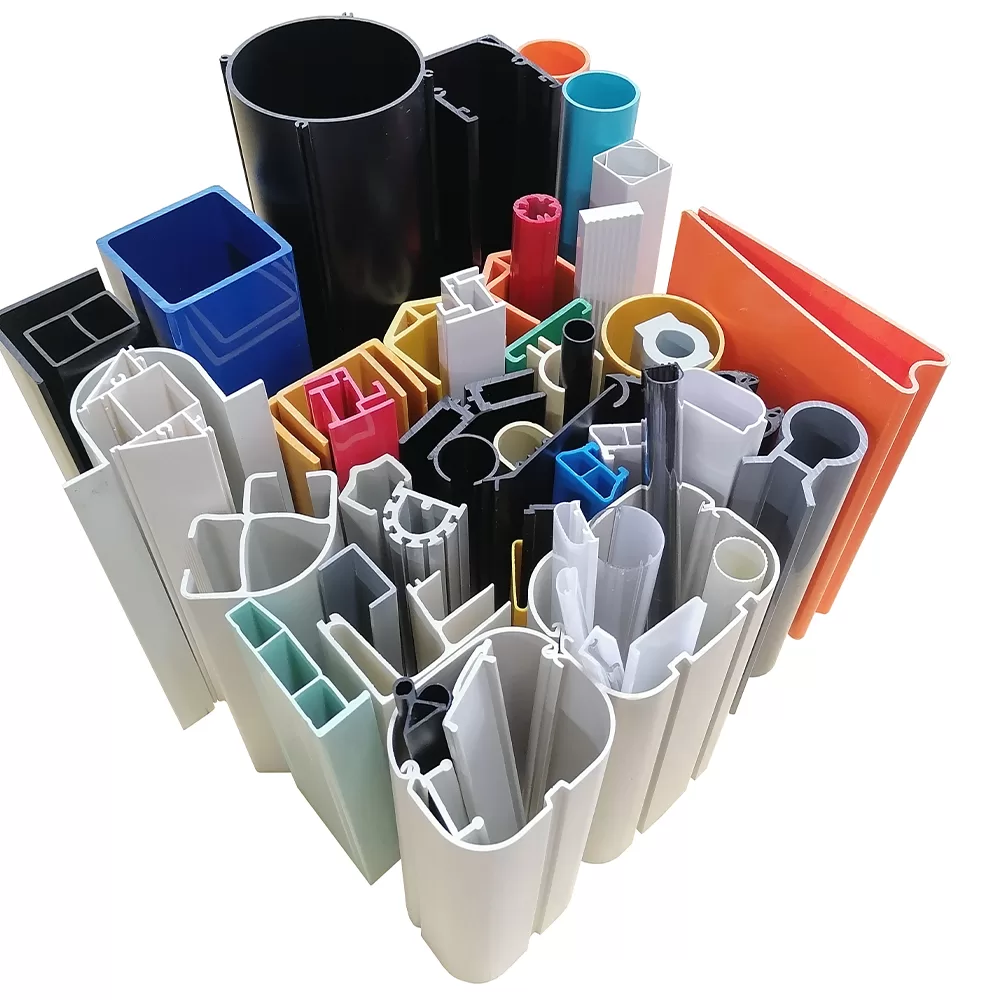
Sorts Of Plastic Suitable for Extrusion
The choice of the best sort of plastic is a vital facet of the extrusion procedure. Various plastics offer one-of-a-kind residential properties, making them more matched to particular applications. Polyethylene, as an example, is generally utilized as a result of its inexpensive and very easy formability. It offers exceptional resistance to chemicals and moisture, making it ideal for products like tubes and containers. Polypropylene is an additional prominent option due to its high melting point and resistance to exhaustion. For even more durable applications, polystyrene and PVC (polyvinyl chloride) are typically chosen for their stamina and toughness. Although these prevail choices, the selection eventually depends upon the particular demands of the item being created. Understanding these plastic types can significantly enhance the extrusion process.
Contrasting Plastic Extrusion to Various Other Plastic Forming Techniques
Recognizing the kinds of plastic appropriate for extrusion paves the method for a wider conversation on just how plastic extrusion piles up versus other plastic developing approaches. Plastic extrusion is unmatched when it comes to producing continuous profiles, such as pipes, seals, and gaskets. It likewise enables for a consistent cross-section along the length of the product.
Secret Advantages of Plastic Extrusion in Manufacturing
In the realm of production, plastic extrusion provides many substantial advantages. One noteworthy advantage is the cost-effectiveness of the process, which makes it an economically enticing production approach. In addition, this technique gives premium product adaptability and boosted production speed, consequently enhancing total production efficiency.
Affordable Production Method
Plastic extrusion leaps to the leading edge as a cost-effective manufacturing technique in manufacturing. Furthermore, plastic extrusion calls for less power than standard manufacturing approaches, contributing to reduced operational costs. In general, the financial advantages make plastic extrusion a highly appealing option in the production sector.
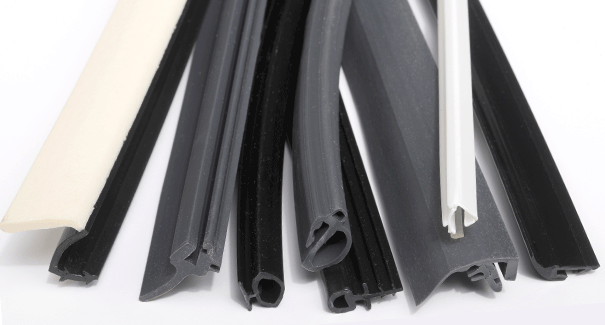
Superior Product Versatility
Beyond the cost-effectiveness of plastic extrusion, an additional substantial advantage in making depend on its premium product adaptability. This procedure permits the production of a vast selection of items with varying sizes, shapes, and designs, from basic plastic sheets to detailed profiles. The adaptability is credited to the extrusion die, which can be customized to yield the wanted product style. This makes plastic extrusion a suitable service for sectors that call for customized plastic components, such as automobile, construction, and product packaging. The capacity to create varied items is not only beneficial in conference particular market needs however additionally in making it possible for manufacturers to discover new product with marginal capital investment. Essentially, plastic extrusion's item versatility cultivates advancement while improving operational performance.
Boosted Production Speed
A significant benefit of plastic extrusion lies in its boosted manufacturing speed. Couple of various other manufacturing procedures important link can match the rate of plastic extrusion. Additionally, the capability to maintain consistent high-speed production without sacrificing product high quality establishes plastic extrusion apart from various other approaches.
Real-world Applications and Impacts of Plastic Extrusion
In the world of manufacturing, the strategy of plastic extrusion holds profound value. The financial benefit of plastic extrusion, largely its high-volume and affordable output, has actually transformed manufacturing. The market is constantly striving for innovations in eco-friendly and recyclable materials, suggesting a future where the advantages of plastic extrusion can be kept without endangering environmental sustainability.
Conclusion
To conclude, visit this web-site plastic extrusion is a very efficient and reliable method of transforming raw products right into varied products. It provides many hop over to these guys advantages over other plastic developing approaches, including cost-effectiveness, high output, very little waste, and design adaptability. Its effect is greatly felt in numerous industries such as building and construction, automobile, and durable goods, making it an essential process in today's production landscape.
Delving much deeper right into the technological process of plastic extrusion, it begins with the choice of the ideal plastic product. As soon as cooled down, the plastic is reduced right into the needed sizes or wound onto reels if the item is a plastic movie or sheet - plastic extrusion. Comparing Plastic Extrusion to Various Other Plastic Forming Methods
Comprehending the kinds of plastic appropriate for extrusion paves the method for a more comprehensive conversation on just how plastic extrusion piles up versus various other plastic developing approaches. Couple of other production procedures can match the rate of plastic extrusion.
Report this page